Customer Stories
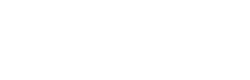
Customer Stories
Business Type: Manufacture of seasonings and sauces
Industry: Food manufacturer
Location: Santa Fe Springs, CA USA
Number of Users: 20
Website: https://www.wakouusa.com/
WAKOU USA INC. – a subsidiary of WAKOU SHOKUHIN CO., LTD. – is a manufacturer of soup bases, seasoning oils and various sauces that develops high quality Ramen soup for the U.S. market.
Their products include a variety of Ramen Soup Base, Ramen Flavor oils, Kara age Marinade Sause and other sauces.
WAKOU’s Ramen soup are used in many Food Services, Ramen Shops, Restaurants and bars. Today, its service has spread across the country in the U.S.
WAKOU USA began manufacturing operations in the United States in 2015. Initially, production items and volumes were limited, but due to the recent ramen boom, sales volume and customers have expanded steadily. With the expansion of production, the simple accounting software they used since the factory’s establishment was no longer able to handle the production controls to ensure food safety, efficient production planning and the management of company-wide business data.
WAKOU USA chose Microsoft Dynamics NAV as their next generation ERP system and asked Calsoft Systems to be their partner for supporting the implementation. With the comprehensive business support functions of Dynamics NAV, WAKOU USA is now having a unified core system that allows various departments to share information, and the management to manage data on the manufacturing floor and in the office. WAKOU USA is now able to get the real time data of the business immediately from the new ERP.
WAKOU USA will be working with the CALSOFT team to find more effective ways to use the system in the future.
“The new system can now create documents for external use in a single step, from order to product delivery and invoicing.”
“As part of internal control, Dynamics NAV made it impossible to proceed to the next step of the process without “posting” at each step, so the unexpected error rate significantly decreased.”
Mr. Kikuchi (WAKOU USA, Chief Financial Officer)
The R&D/Sample Request management is now able to manage version history by introducing the NAV system instead of the conventional paper-based procedure.
It is now possible to do in-depth data analysis for sales data aggregation and trend analysis.
Better control of inventory movement in shop floor and warehouse.
By utilizing mobile WMS application that works seamlessly with Dynamics NAV, Operators in the production floor and warehouse can now prevent picking of wrong raw materials mistakenly.
Sales/sales data and production management are organically linked to improve production planning activities, obtaining recommendations from the system that lead to optimal purchasing and production planning.
When a recall occurs, it is essential for a food manufacturer to know the route from the raw material to the finished product. With Dynamics NAV’s fine-grained inventory management function, raw material lots, WIP lots, and product lots are all linked, so they can respond immediately in case of a recall.
In addition to the standard functions of Dynamics NAV, CALSOFT’s recipe R&D management function has been implemented, allowing the database of past prototypes to be effectively utilized in new product development and customer proposal activities.