Industry 4.0 refers to the fourth phase in the Industrial Revolution that focuses on interconnectivity, automation, machine learning, and real-time data.
Intelligent networking of machines and processes for the industry with the help of information and communication technology is changing how manufacturers do business. Simply said, it is the digital transformation of manufacturing. It gives you access to the real-time data and insights you need to make smarter, faster decisions about your business, which can ultimately boost the efficiency and profitability of your entire operation.
What are examples of Industry 4.0 technologies?
Examples of Industry 4.0 related technologies that are becoming more prominent on factory floors include:
- The Internet of Things (IoT)
- The Industrial Internet of Things (IIoT)
- Smart Manufacturing
- Connected Manufacturing
- Smart Factories
- Cloud Computing
- Cognitive Computing
- Artificial Intelligence
- Cyber-physical Systems (CPS)
Businesses and supply chains already use some of these advanced technologies, but the full potential of Industry 4.0 comes to life when used together.
The Evolution of Industry from 1.0 to 4.0
To understand the impact of the concept of Industry 4.0 on manufacturing processes, it’s important to understand the evolution of the industry from 1.0 to 4.0.
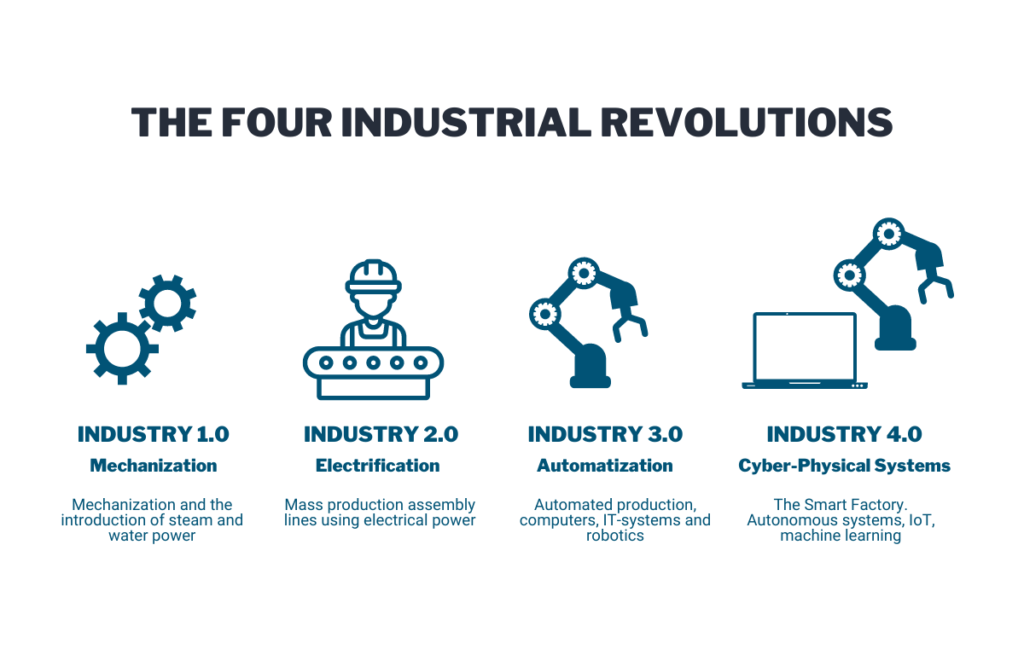
Industries Affected by Industry 4.0
All manufacturers, suppliers, and other parties in the supply chain have been affected by Industry 4.0. It has opened up new possibilities and opportunities for custom manufacturers to create, design, and manufacture custom products while maintaining efficiency and profitability.
How is Industry 4.0 used in manufacturing?
Supply chain management
Smart manufacturing operates on Internet-connected machinery to monitor the production process. It identifies opportunities for automating operations and uses data analytics to improve manufacturing performance.
Preventive Maintenance
Industry 4.0 solutions and a connected factory floor can forecast downtime in machinery before it occurs. In addition, industry 4.0 systems detect problems before they arise and can provide insight on how to solve issues before they become a problem.
Tracking and Optimization
Industry 4.0 technology makes it easier for businesses to track inventory, quality, and optimization opportunities related to logistics. Connected manufacturing and the IoT provide employees with an overview and visibility over company assets worldwide. As a result, adjustments can be streamlined and managed centrally and in real-time.
What are the benefits of Industry 4.0?
The benefits of Industry 4.0 include improved productivity and efficiency, better flexibility and agility, and increased profitability. Some key benefits of Industry 4.0 companies experiencing are:
- Improved Productivity and Efficiency: Businesses are making data-driven decisions across their operations, improving forecast accuracy, supporting on-time delivery, and building profit-optimized plans.
- Flexibility and Agility: It’s easier to scale production up or down in a Smart Factory as well as introducing new products to the production line.
- Better Customer Experience: The customer experience will enhance with automated track and trace capabilities.
- Innovation opportunities: Better knowledge of the manufacturing process leads to opportunities to innovate.
- Green and Sustainable Solutions: Less resources, material, and product waste will both lead to an increased probability and a more sustainable solution.
How can Industry 4.0 benefit from an ERP system?
Using Industry 4.0 technologies in ERP systems will allow organizations to gain better visibility into manufacturing processes and supply chain activities. They can optimize their logistics operations, improve inventory tracking, and efficiently manage their workforce with automated resource planning.
Conclusion
The main objectives of Industry 4.0 are to make manufacturing and related industries faster, more efficient, and more customer-centric while using automation and optimization to detect new business opportunities and models.
An Industry 4.0-ready ERP platform like Microsoft Dynamics 365 Supply Chain Management will help you benefit your supply chain by improving planning and processes to reduce waste, move more efficiently and improve margins. Manufacturers can integrate any manufacturing execution system (MES) in real-time and leverage AI and machine learning to develop competitive advantages.
Ready for your company’s digital transformation?